Les 25 meilleures formations RSE : notre sélection
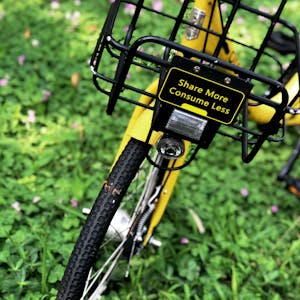
ACC’s mission is to accelerate the transition to sustainable and affordable mobility for all, significantly reducing greenhouse gas emissions through producing batteries in Europe.
Produits ou services responsables
La mission de cette entreprise est de concevoir des produits ou proposer des services éco-responsables alignés avec les besoins de la transformation écologique et solidaire.
Join us and be a pioneer for a green transport revolution.
Automotive Cells Company (ACC) is one of Europe’s newest and most exciting high-tech companies. Backed by Saft-Total, Stellantis and Mercedes-Benz, ACC is set to power the future of the automotive industry by innovating in battery technology.
We aim to produce sustainable, affordable, high-capacity, longer-life batteries as a cleaner alternative to current energy sources. We have created an R&D center and new state-of-the art facility in Nouvelle Aquitaine, France, and we are building gigafactories in Germany and Italy, in addition to the one already built in Hauts de France.
We need a range of skilled and agile people to bring our vision to life, especially in the areas of industrialization, mechanical design, testing/prototyping and any other function of a new-born company. If you’re looking to take your career further than you imagined, if you’re passionate about creating cleaner transport, we’d like to hear from you.
Our core Values are : Pioneering Spirit, Fast & Agile, Excellence, Greener & Cleaner !
Accelerating sustainable mobility for all.
Some of our assets: A production site 30 minutes from Lille, connected to Paris, Bruxelles and London by highways and TGV, equipped with cutting-edge technologies, in an international environment and surrounded by green spaces.
You will be working in the first Gigafactory in France, and benefit from charging stations for electric vehicles, catering service delivered (with 7 euros/day paid by the employer), complementary retirement plan (subject to a salary threshold), additionnal & seniority leaves, free access to Gofluent, etc
https://www.acc-emotion.com/fr/facilities/billy-berclau
ACC Billy-Berclau Gigafactory - presentation
https://www.youtube.com/watch?v=1D_aFw2GPOY&t=1s
Our process usually involves 3 interviews: 2 technical and one HR.
Tu souhaites te réorienter mais tu ne sais pas par où commencer ? Pas de panique, on te propose une sélection de formations aux métiers de la transition écologique et solidaire !
Tu ne t'épanouis plus dans ton travail, et tu envisages de changer de profession pour trouver plus de sens dans ta vie professionnelle ? Découvre les ressources pour t'aider à réflechir à un projet de reconversion et trouver ta voie.