Entrepreneurship in the territories: is it the right time?
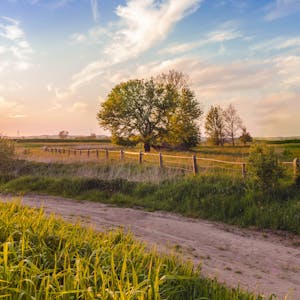
ACC’s mission is to accelerate the transition to sustainable and affordable mobility for all, significantly reducing greenhouse gas emissions through producing batteries in Europe.
Responsible products or services
The company's mission is to design eco-responsible products and services aligned with the needs of the ecological transformation.
Join us and be a pioneer for a green transport revolution.
Automotive Cells Company (ACC) is one of Europe’s newest and most exciting high-tech companies. Backed by Saft-Total, Stellantis and Mercedes-Benz, ACC is set to power the future of the automotive industry by innovating in battery technology.
We aim to produce sustainable, affordable, high-capacity, longer-life batteries as a cleaner alternative to current energy sources. We have created an R&D center and new state-of-the art facility in Nouvelle Aquitaine, France, and we are building gigafactories in Germany and Italy, in addition to the one already built in Hauts de France.
We need a range of skilled and agile people to bring our vision to life, especially in the areas of industrialization, mechanical design, testing/prototyping and any other function of a new-born company. If you’re looking to take your career further than you imagined, if you’re passionate about creating cleaner transport, we’d like to hear from you.
Our core Values are : Pioneering Spirit, Fast & Agile, Excellence, Greener & Cleaner !
We are also very proud of our 2022 CSR Report : https://www.acc-emotion.com/stories/accs-2022-corporate-sustainability-report
Accelerating sustainable mobility for all.
The Maintenance Method Manager leads the deployment and application of equipment maintenance standards.
In this capacity, he's the on-site guarantor of the maintenance guidelines and processes. He ensures that the personnel concerned (managers, technicians, professionals, operators) are properly trained and that the processes are properly applied. He evaluates the site's performance and manages the associated progress plans.
His perfect mastery of the maintenance professions and processes enables him to participate in the upstream structuring choices and sizing (projects), to assist the operational staff in the operating phase, and also to carry out RETEX downstream in order to contribute to the continuous improvement of the SMM (reference systems and their application). He will also manage the performance of maintenance services in all areas (regulatory controls, equipment maintenance, specific expertise, repairs, spare parts supply and warehouse management, for example).
His overall view of the entire site will enable him to prioritise and arbitrate the maintenance OVERHAUL, but also to manage the deployment of innovative tools (technical and/or methodological). In this capacity, he will ensure the efficient deployment of Maintenance 4.0.
Main tasks
Maintenance training. Troubleshooting, implementation of palliative and curative measures. Reading of plans, diagrams (electrical, pneumatic, etc.). Methods of 5P analysis, MAXER, etc... and continuous improvement (Kaizen, TPM, etc...).
Maintenance of automated industrial production systems, ideally in high speed. Experience of more than 5 years as minimum; more than 10 years appreciated.
Logic, analytical skills, autonomy.
Pedagogical, teamwork, attention to detail. Tenacity.
Join us in the first Gigafactory in Italy, in the beautiful town of Termoli, take the chance to work in an international environment and be a pioneer of the green transport revolution. We offer a competitive salary, bonus scheme and access to our canteen.
Our process usually involves 3 interviews: 2 technical and one HR.
Per questa ricerca, sarà data priorità, previa verifica dei requisiti professionali, all'assunzione di lavoratori che siano:
1. beneficiari di interventi di sostegno al reddito;
2. disoccupati a seguito di procedure di licenziamento collettivo;
3. lavoratori di aziende del Molise coinvolte in tavoli di crisi attivi presso il Ministero dello Sviluppo Economico.
I requisiti professionali includono il percorso di formazione professionale e le competenze e capacità acquisite, e si terrà conto delle competenze relazionali e della qualità professionale in termini di conoscenze, capacità e abilità, in relazione alla mansione e al contesto organizzativo.
Discover all the resources to inspire and guide you in the world of positive impact. Testimonials, analyses, job descriptions and skills of tomorrow, everything you always wanted to know without daring to ask.
You no longer thrive in your work, and you plan to change profession to find more meaning in your professional life? Discover the resources to help you think about a retraining project and find your way.